Opportunities with biocomposite and WoodSafe®
WoodSafe ® is made from a biocomposite that is optimized to replace a wide range of polymers and can also achieve very high tensile strength. The advantages of the polymer are formability, durability, flexibility and design freedom. The advantages of wood fiber are its strength, natural look/feel, renewable raw material and low CO 2 footprint.
Biocomposite is a uniquely developed biocomposite material that combines these advantages. WoodSafe ® hazardous waste containers have optimized the mix of wood fiber and polymers with the goal of meeting the requirements for these containers according to UN tests, while minimizing climate impact. FrostPharma has patented (patent pending) these hazardous waste containers as they have managed to find a solution (process and design) to manufacture the WoodSafe ® product series.
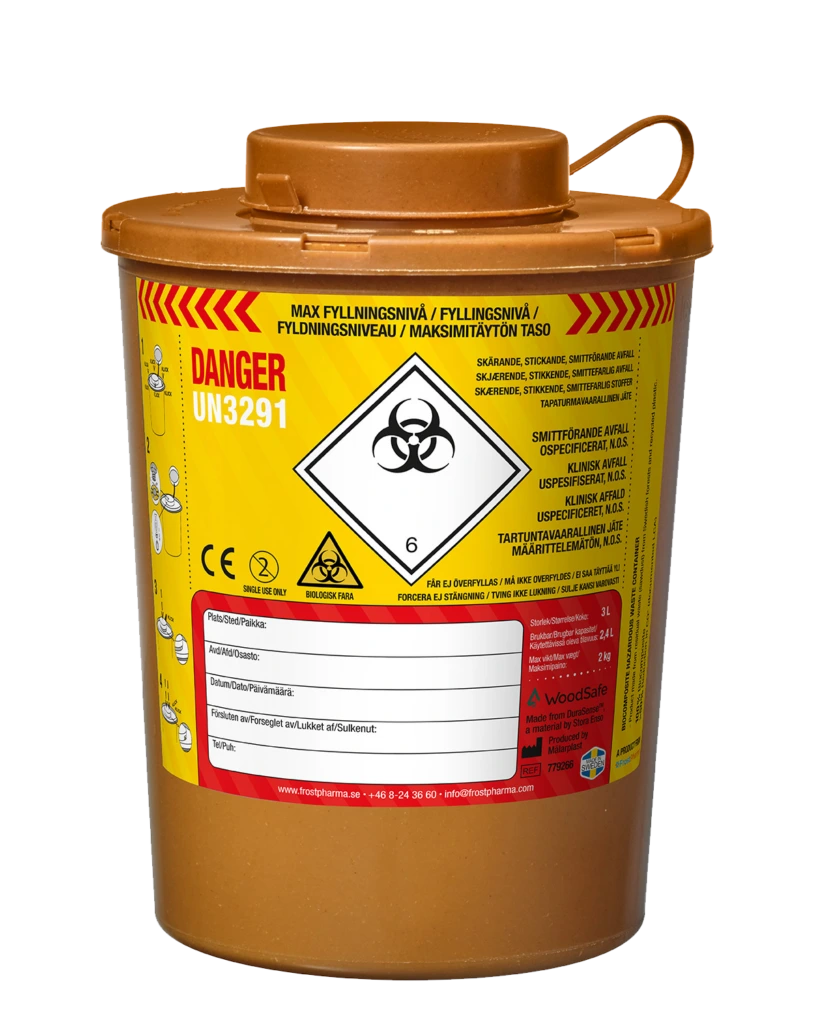
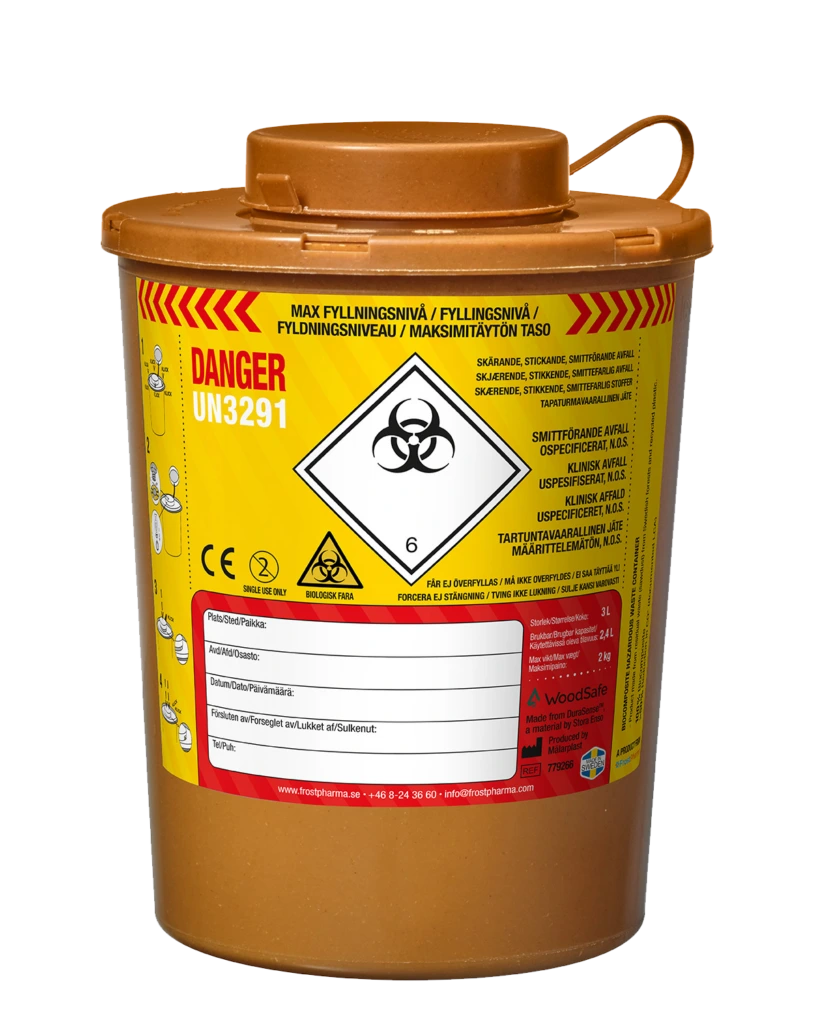
Opportunities with biocomposite and WoodSafe®
WoodSafe® is made of biocomposite from Stora Enso. Stora Enso's biocomposite is optimised to replace a wide range of polymers and it can also achieve very high tensile strength. The advantages of the polymer are formability, durability, flexibility and design freedom. The advantages of wood fibre are its strength, natural look/feel, the fact that it is a renewable raw material and its low CO2 footprint.
DuraSense® is a uniquely engineered biocomposite material that combines just these benefits. WoodSafe® hazardous waste receptacles have optimised the mix of wood fibres and polymers with the aim of meeting the requirements of these receptacles according to UN tests, while minimising the climate impact. FrostPharma has patented (patent pending) these hazardous waste containers as they have managed to find a solution (process and design) to produce the WoodSafe® product line.
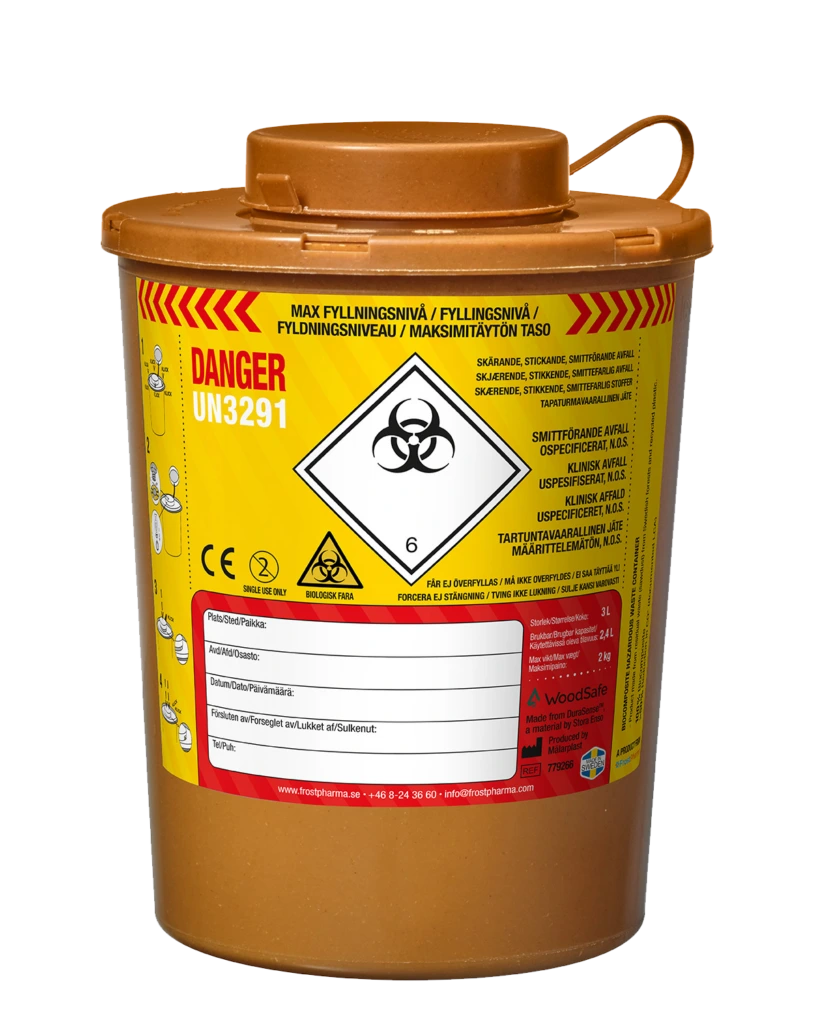
Opportunities with biocomposite and WoodSafe®
WoodSafe® is made from Stora Enso biocomposite that is optimised to replace a wide range of polymers and can also achieve very high tensile strength. The advantages of the polymer are formability, durability and flexibility and design freedom. The advantages of wood fibre are its strength, natural look/feel, the fact that it is a renewable raw material and its low CO2 footprint.
Stora Enso's biocomposite is uniquely designed to combine these benefits. WoodSafe® hazardous waste containers have optimised the mix of wood fibres and polymers with the aim of meeting the requirements for these containers according to UN tests, while minimising the climate impact. FrostPharma has patented (patent pending) these hazardous waste containers as they have managed to find a solution (process and design) to manufacture the WoodSafe® product line.
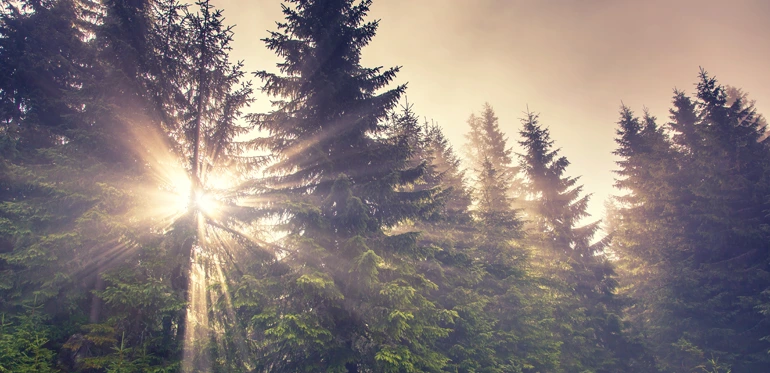
Bioplastics and biocomposites
What requirements should and can be placed on bioplastics/biocomposites today. According to the 2030 Agenda, we need to shift to the use of more sustainable materials in order to achieve the climate change mitigation goals. For example, plastics with fossil raw materials should be replaced by bio-based or recycled raw materials.
Plastic products should be made from bio-based raw materials that are not grown on land where the raw material competes with food production or which was previously rainforest land. Requirements for percentage content of bio-based raw materials should be set as high as possible based on the current situation. From a life cycle perspective, the products must have a demonstrably low/lower climate impact, which is demonstrated by LCA or equivalent analysis.
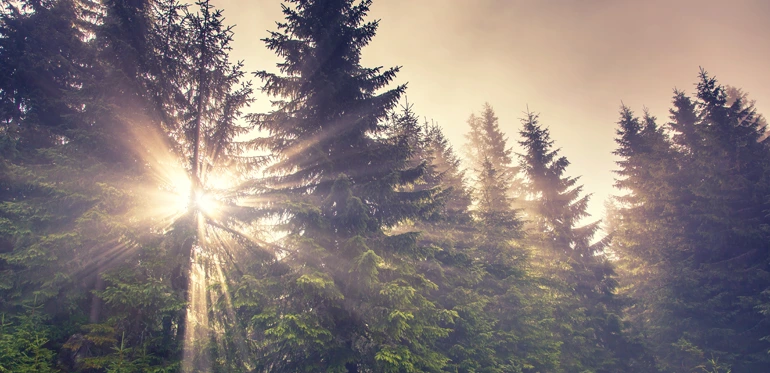
Bioplastics and biocomposites
What requirements should and can be placed on bioplastics/biocomposites today. According to the 2030 Agenda, we need to shift to the use of more sustainable materials in order to achieve the climate change mitigation goals. For example, plastics with fossil raw materials should be replaced by bio-based or recycled raw materials.
Plastic products should be made from bio-based raw materials that are not grown on land where the raw material competes with food production or which was previously rainforest land. Requirements for percentage content of bio-based raw materials should be set as high as possible based on the current situation. From a life cycle perspective, the products must have a demonstrably low/lower climate impact, which is demonstrated by LCA or equivalent analysis.
3rd largest source of CO2 emissions
Hazardous waste containers of different sizes are today a large part of plastic consumption in healthcare. After examination gloves and disposable aprons, hazardous waste containers are the largest product in the number of tonnes per year that go to incineration. By replacing today's hazardous waste containers with biocomposite materials, we are halving the carbon footprint of one of the largest plastic items.
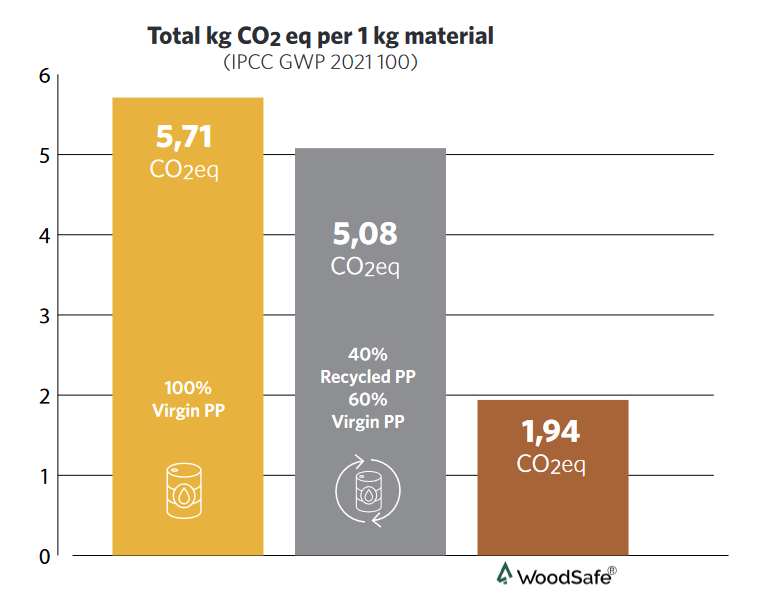
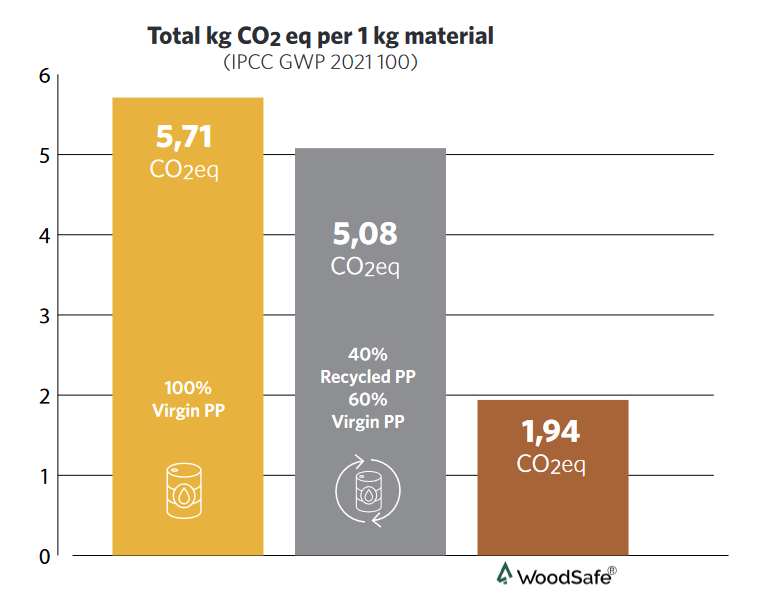
3rd largest source of CO2 emissions
Hazardous waste containers of different sizes are today a large part of plastic consumption in healthcare. After examination gloves and disposable aprons, hazardous waste containers are the largest product in the number of tonnes per year that go to incineration. By replacing today's hazardous waste containers with biocomposite materials, we are halving the carbon footprint of one of the largest plastic items.